BYAM England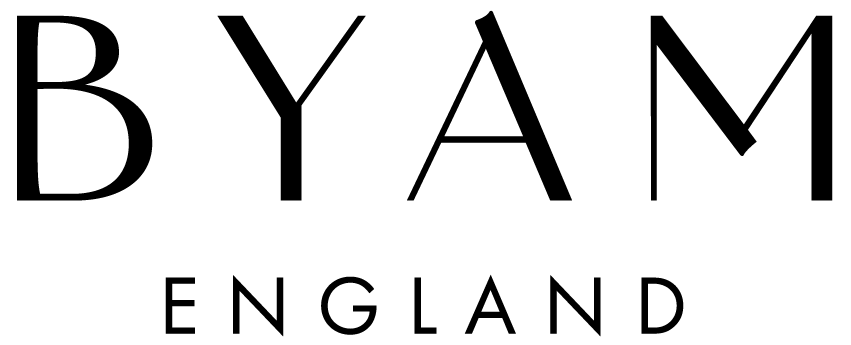
Store access
Opening soon
Hello,, apologies for the inconvenience of finding our website closed, as you know we are a small family business and we are taking a late summer break, business will resume week commencing 13th October. Thank you so much for your patience and understanding and in the meantime, should you have any enquires ,please do reach out by email at hello@byamengland as our emails will still be read. Thank you x